INTRODUCTION
Engine fuel supply system covers the quality and quantity of fuel, air and air fuel mixture flow and combustion aspects in efficient operation of an engine by performing following functions. The fuel system covers the travel of fuel from the fuel tank to injection of atomized fuel into the combustion chamber/cylinder where the burning of fuel takes place to generate mechanical work output. Various components like fuel tank, fuel feed pump, fuel pipes, fuel filters, fuel pump, high pressure pipes, injecting nozzles are the components of fuel line to be discussed in this module.

Fuel storage
Fuel tank is usually made up of metal or fibre sheet having anti rust and better heat and shock resistant properties. Fuel tank should prevent fuel to get contaminated with dust, water or any other foreign material. These impurities in the fuel can block the passage of fuel through the pump and nozzles which further stop the engine.
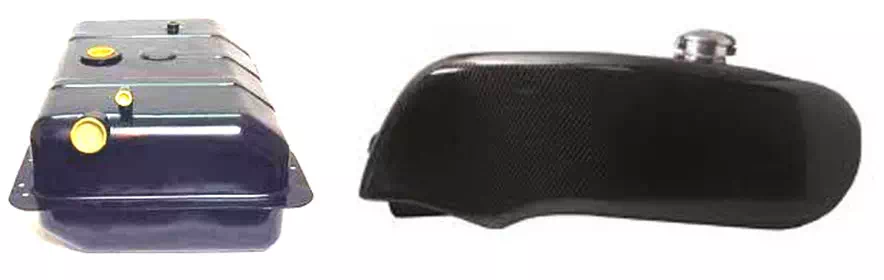
Fuel Filtering
Fuel filters (primary & secondary) are provided to remove the impurities (water or dust) from the fuel while flowing from tank to reach fuel injection pump. Primary filter is usually made of wire mesh and used for removing the coarse particles. It is attached to the fuel feed pump.
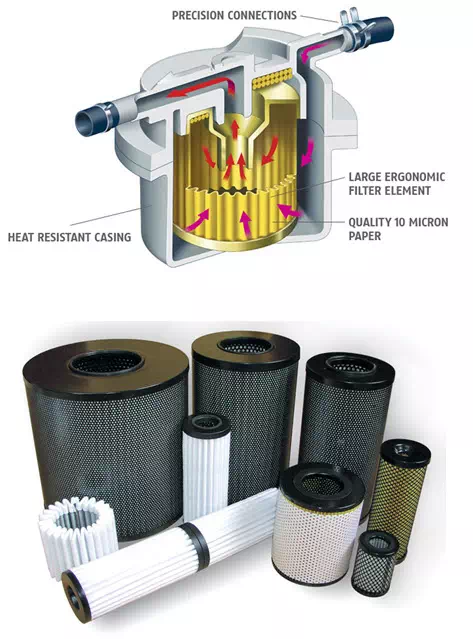
Further to remove the fine particles and abrasive material in the fuel, secondary filter is used which is made of fine pores and it is placed after the fuel feed pump. These smallest impurities are retained to protect the extremely sensitive parts like fuel pump and injectors to get damaged. These filters are generally made of two sections/stages in which first stage is made of cloth and second is of paper through which the fuel passes to leave impurities behind in the fuel line.
Air Cleaners
Since the air fuel mixture is to be burnt in the combustion chamber of the cylinder, just like fuel being filtered, air should also be filtered and cleaned before entering into the cylinder. The dust particles in the air when mixed with oil act like abrasive material which deteriorates the cylinder walls or liners, pistons or rings and hence decrease the engine performance. The characteristics of an ideal air cleaner include high efficiency in dust removal from air, small restriction to the air flow, small and simplicity in design and easy to mount, clean and low in cost. The location of air cleaner on the vehicle affects cleaning efficiency and it is one of the most important design parameter to be kept in mind while designing and developing the product. The dust concentration is maximum near the engine and is least in the region exactly above the engine. Hence, the air cleaners are mounted directly above the engine housing. Since, tractors are to be operated in the fields where dust is always significantly high, periodic cleaning of air cleaner becomes very important and essential to have maximum and consistent engine efficiency.
Oil bath type air cleaner
It consists of wire mesh element and oil reservoir at the bottom. The atmospheric air enters the air-cleaner through the windows at the top with a swirl action where some impurities are retained in the pre air cleaner chamber. The air passes through the air duct to the surface of oil bath and the air is reflected upward from the surface oil. The small impurities like dust and chaff etc. stick to the oil surface and are separated from the air. Then the air starts moving upward and passes through the mesh which further cleanse the air and oil drops in the air are separated while passing through this mesh. The left over impurities are also retained by the mesh and get settled in oil bath. These oil bath/bowl and pre cleaner chambers are to be cleaned periodically depending upon the dust conditions. The level of oil is to be maintained at a specific level, because the oil above the desired level results in restricting the air flow and might result in carrying/moving the oil with air reaching engine cylinders. This may lead to increase in sudden increase in speed and sometimes can cause damage to the engine components also.
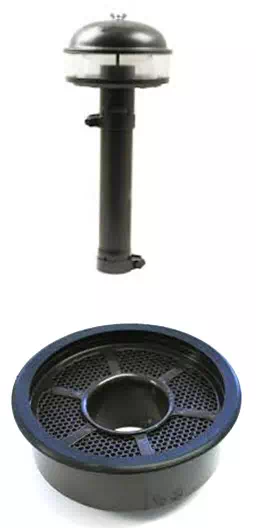
Dry air cleaner
This type of air cleaner consists of a paper filter element with a row of plastic fins around it. As the air from the atmosphere enters the cleaner, the plastic fins give it a high rotational speed between the casting and the filter element. This causes impurities to separate out from air due to centrifugal action, which are thrown out to the casting walls from these flow down. Air without these dust particles then passes through the paper element, which removes any further impurities and clean air then goes to the engine.
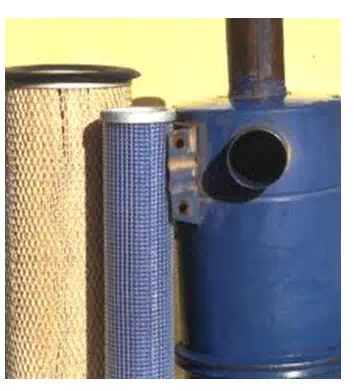
Comments are closed.